BLOW
ブロー成形|特徴・製品事例・不良対策方法など
日本容器のブロー成形技術・成形機
金型製作から製品製造まで一貫対応
金型製作
他社設備でもブロー成形の
金型を制作致します。
試作品製造
開発段階からの
ご相談もお受けいたします。
製品製造
小ロットからの製造が可能です。
成形機製造・メンテナンス
新規成形機の製造から他社製の
メンテナンス、カスタマイズも可能です。
日本容器ではブロー成形、射出成形やインサート成形など幅広く取り扱っておりますが、特にブロー成形を得意としております。
中空製品の仕上がりを左右する空気量の調整や加工ノウハウを保有しているだけでなく、お客様の課題に合わせた成形品の形状提案も可能です。
・ブロー成形品やインジェクション成形品を組み合わせた複雑な形状の製品製造
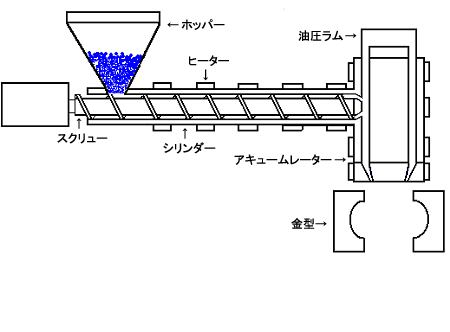
保有設備
タイプ | 台数 | メーカー | |
---|---|---|---|
ブロー成形機 | 65mm | 3 | ブラコー |
80mm | 6 | KTK | |
80mm | 8 | 自社 | |
90mm | 1 | ブラコー |
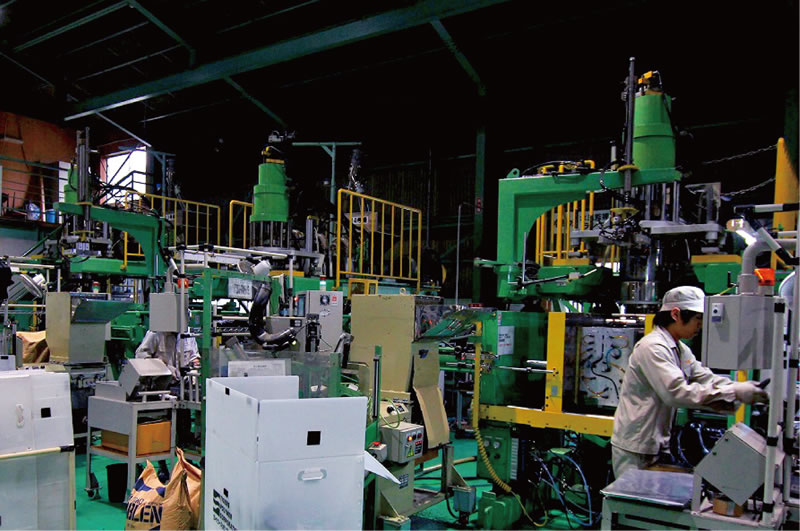
製品事例
ブロー成形とは?
ブロー成形の概要
ブロー成形とは、原料を溶融可塑化して形成されたパリソンと呼ばれる中空前駆体の中空部に、金型内でノズルを通して圧縮空気を吹き入れることにより,中空製品を成形することを指し、その原理は古くからあるガラス瓶の製造方法とほとんど同じです。また、その特徴から中空成形とも呼ばれ、中空製品の成形加工時によく使用されます。
ブロー成形の製造工程
ブロー成形は大きく分けると、以下の3工程で構成されます。
①押出工程
押出工程は原料(プラスチック樹脂)を均一に溶融可塑化し、金型へ送る工程です。
②パリソン形成工程
金型内に樹脂を円筒状に押し出した予備成形状態にする工程です。
③吹込み・冷却工程
出てきたパリソンは型締装置で金型内で締め付けられます。そこで、内部に圧縮空気を吹き込むことで、冷却した金型の内壁に樹脂を押しつけ、金型内部の樹脂を冷却・固化させます。その後、金型を開き、成形品を取り出します。
ブロー成形品の用途、製品事例
製品用途(導入分野)
上述のように、身近な日用品を含む小型容器、大容量の大型容器、そして、各種工業部品まで多岐に渡っており、中身が空洞になっている構造が特徴となります。
・小型容器:洗剤容器、化粧品容器、食品容器(ペットボトル、乳酸飲料容器)など
・大型容器:ガソリンタンク、ドラム缶など
・工業部品:スポイラー、エアコンダクト、ノズルデフロスター、バンパーなど
ブロー成形の種類
一概にブロー成形といっても、さまざまな種類が存在します。以下にいくつかご紹介します。
①押出ブロー(ダイレクトブロー)成形
押出機で樹脂を加熱・可塑化させ、金型より押し出された円筒状のパリソンを冷却・固化させずに、ダイレクトに金型で挟み込み、溶融状態で空気を吹き込んで成形する方法です。
この方法はポリエチレン・ポリプロピレン・塩ビなどの材料に適用され、洗剤・化粧品などの小型容器、ガソリンタンク・ドラム缶などの大型容器、スポイラー・ダクトなどの各種工業部品の製造に広く使用されています。
②射出ブロー成形
射出成形で成形したパリソンを金型に移し、半溶融の状態で空気を吹き込んで成形する方法です。ポリスチレンを材料とした乳酸飲料容器やポリエチレンテレフタレートを材料としたペットボトルなどの製造に使用されています。
③延伸ブロー成形
分子を配向させることによる透明性・剛性・ガスバリヤー性などの性能向上を目的としたものであり、射出成形または押出成形で作られたパリソンを、分子が配向し、かつ製品が均一に延伸される温度に再加熱し、縦方向はロッドにより機械的に伸長し、横方向は空気の吹き込みにより膨張させ、2軸方向に延伸配向させる成形方法です。材料にはポリエチレンテレフタラート・塩ビ・ポリプロピレンなどが用いられ、炭酸飲料や醤油などの食品関係容器、医薬品容器の製造に使用されています。
よく用いられる原料
上述のように、プラスチック樹脂が用いられ、成形方法によって異なりますが、代表的なものとして、以下が挙げられます。
ポリエチレン、ポリプロピレン、ポリスチレンなど。
ブロー成形の特徴
ブロー成形は、成形品の外面でのみ金型と接触するため(内面は空気で圧力を掛けているだけで接触しない)、金型全面に接触する射出成形などは異なり、簡易的で修正がしやすい構造となり、短納期で製作することが可能です。特に、短い開発期間内で設計変更を余儀なくされる自動車業界では、非常にメリットが大きい成形方法と言えます。
ブロー成形のメリットとデメリット
ブロー成形のメリット
代表的なものとして、以下が挙げられます。
①製品が軽量
こちらも成形プロセス上、プラスチック原料を用い、また中空製品となるため、比較的軽量な製品となります。
②金型製作費用が安価
金型の部品点数が少ない故構造がシンプルとなり、その分金型費用が抑えられ、安価に製作が可能です。
ブロー成形のデメリット
代表的なものとして、以下が挙げられます。
①形状の制約がある
吹き込んだ空気の圧力で成形するため、形状でエッジの多いものや丸みの部分が小さいもの、急激に尖ったような複雑な形状は困難です。このような形状は肉厚精度が特に悪くなりやすく、安定的な生産が難しくなります。
②肉厚精度が悪い
空気の圧力で樹脂を金型内壁に押し付けるため、接触面全てを均一に冷却するように制御することが難しく、肉厚精度が悪くなりやすいです。そのため、はめ合い公差が厳格な高品質を要求される製品では注意が必要です。
ブロー成形特有の不良とその解決策
ブロー成形の工程で発生する種々の成形不良現象は、成形品となる最終製品の品質に大きな影響を与えます。代表的なものとして、以下が挙げられます。
偏肉
押出工程で生じるドローダウンという成形不良現象は、「偏肉」という成形品の上部と下部で厚みが不均一となる形状欠陥を招くことがあります。なお、ドローダウンとは、溶融した樹脂が重力方向に垂れ下がる現象のことで、溶融樹脂の粘度が低い場合などに発生しやすくなります。この偏肉を防止するためには、樹脂粘度や樹脂温度、吹き入れる空気圧の調整などが必要となります。
肌荒れ
パリソン形成工程で生じるメルトフラクチャーという成形不良現象は、成形品の「肌荒れ」という表面欠陥を招くことがあります。
なお、メルトフラクチャーとは、パリソン押出時に溶融樹脂の流動状態が乱れる現象のことで、具体的には押出速度を上げていった場合にパリソン表面がネジ山状になったり、パリソン全体が不規則に捩れたりすることがあり、樹脂の持つ弾性的性質の影響が大きいと言われています。
この肌荒れを防止するためには、低粘度の樹脂を使用したり、押出量の調整などが必要となります。
気泡
パリソン形成工程で空気やガスなどを巻き込んでしまうと、「気泡」という外観不良を招き、透明容器の場合の外観不良に加え、応力集中による割れ不良を引き起こす原因にもなります。
なお、気泡とは、樹脂の内部に空洞が発生する現象のことで、空気などが巻き込まれやすい成形条件であると発生しやすくなります。この気泡を抑制するためには、押出量や成形温度の調整、金型にエア抜き機構を設けることなどが必要となります。