INJECTION
射出成形(インジェクション成形)|特徴・製品事例・不良対策方法など
日本容器の射出成形技術
日本容器では、射出成形品の試作開発から量産まで承ります。
・ガラス入りPPなどの特殊な素材の射出成形
・ブロー成形品やインジェクション成形品を組み合わせた複雑な形状の製品製造
・射出成形と溶着の組み合わせによる容器型製品の製造
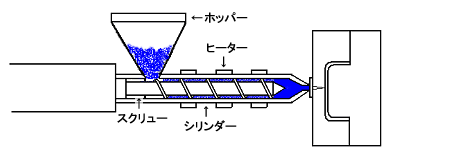
保有設備
タイプ | 台数 | メーカー | |
---|---|---|---|
射出成形機 | 450トン | 1 | 東洋機械金属 |
550トン | 1 | JSW | |
650トン | 2 | JSW |
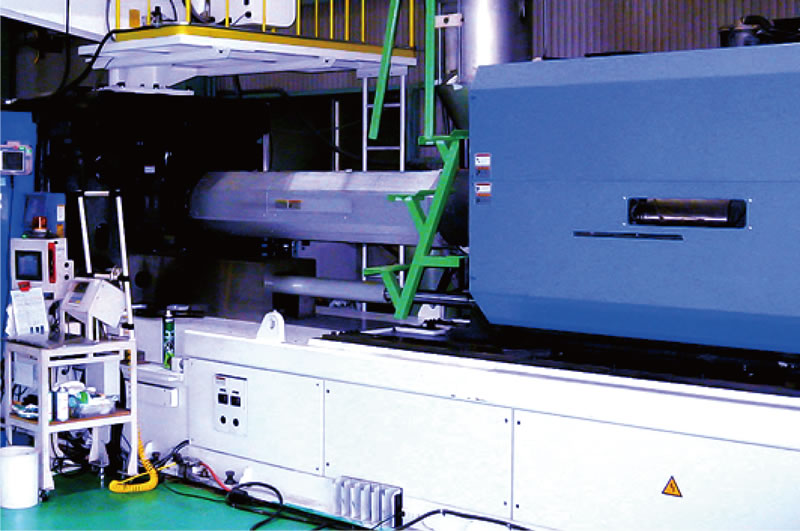
製品事例
射出成形(インジェクション成形)とは?
射出成形の概要
射出成形とは、溶融可塑化したプラスチック原料を金型内に注射のように注入し、充填することで樹脂製品を成形することを指し、プラスチックの最も一般的な成形法の一つです。また、肉厚の薄いものや複雑な形状などさまざまな樹脂製品を高精度かつ高速に成形できるため、大量生産に適した方法になります。
射出成形の製造工程
射出成形は大きく分けると、以下の3工程で構成されます。
①押出工程
押出工程は原料(プラスチック樹脂)を均一に溶融可塑化する工程です。
②金型注入工程
溶融樹脂に圧力をかけて金型内に注入し、充填する工程です。
③冷却工程
金型内部の樹脂を圧力をかけた状態で冷却・固化させます。その後、金型を開いた後、成形品を突き出し、取り出します。
射出成形品の用途、製品事例
製品用途(導入分野)
上述のように、機械部品などの小型製品、PC関連・電子機器などの中型製品、そして、家電製品や自動車部品を含む大型部品まで多岐に渡っており、微細であったり、精密性が高いことが特徴となります。
・小型製品:スマートフォンのカバー、テレビゲーム機のコントローラー、プラモデル、ドライバーやハサミの取っ手部分など
・中型製品:電機製品の筐体、トイレの便座など
・大型製品:テレビ、プリンター、洗濯機、自動車のバンパーなど
射出成形の種類
一概に射出成形といっても、さまざまな種類が存在します。以下にいくつかご紹介します。
①インサート成形
金型内にあらかじめ金属製のネジやコネクタピンなどのインサート部品を置いておき、その周囲にプラスチック樹脂を注入し、一体化成形する方法です。
この方法は、プラスチックの絶縁特性を活かしたコネクタやスイッチなどの電子部品、また、ドライバやラジオペンチなどの工具の製造に広く使用されています。
②二色成形
1つの射出成形機の中に装着された2つの金型内に、材質や色の異なる2つの樹脂を射出して、一体化成形する方法です。
この方法は、組み立てにかかる人件費や工程を削減することができるので、コスト低減が可能であり、多様な機能追加による製品の付加価値も向上できます。インシュレータやサイドスポイラーなどの自動車部品からキーボードなどの電化製品まで広く使用されています。
③低圧成形
金型内の圧力を低く保持して成形する方法です。
この方法は、圧力を下げることでエアベントが良好となり、バリやソリなどが少ないのが特徴です。
ポリ塩化ビニルを材料とした自動車用ドアガード、バンパーなどの製造に広く使用されています。
よく用いられる原料
上述のように、プラスチック樹脂が用いられ、成形方法によって異なりますが、代表的なものとして、以下が挙げられます。
ポリ塩化ビニル、ポリアセタール、ナイロン、ABS樹脂、ポリプロピレン、ポリエチレン、ポリスチレン、ポリカーボネート。
射出成形の特徴
射出成形は、ブロー成形同様、安価で成形品形状の自由度が高いプラスチック樹脂を原料にするため、大量生産に適した成形手法です。また、複雑形状を得意としており、最も汎用性・応用性に優れ、高精度で高品質な成形方法となります。
さらに、近年はCAEや自動化技術が普及し、一度成形条件を決めてしまえば、ほぼ通年、同じ成形条件で同品質の製品を作ることが可能です。
射出成形のメリットとデメリット
射出成形のメリット
代表的なものとして、以下が挙げられます。
①大量生産が可能
成形プロセス上、ハイスピードで生産が可能であるため、早く大量に生産が可能で大ロット生産向きです。さらに、金型に複数分のキャビティ(金型内部の凸部空洞)が彫ってあれば、一度の成形で複数の製品を生産することもできます。
②形状の自由度に優れる
金型の形を変えれば、複雑で精巧な形状の成形も可能であり、プラモデルのネジのような小型製品から、トイレの便座のような中型製品や自動車のバンパーのような大型製品まで、多種多様なサイズ・形状の製品を作ることができます。
③仕上げ加工がほぼ不要
製品の表面性は金型の表面性に依存するため、金型を鏡面仕上げにすれば、製品の表面にツヤツヤの光沢を持たせることができるため、成形後の仕上げ加工は必要に応じてバリ取りを行う程度で、ほとんど不要です。
射出成形のデメリット
代表的なものとして、以下が挙げられます。
①小ロット生産に不向き
早く大量に生産が可能である反面、設備が大掛かりとなり、小ロット生産には不向きです。
②形状の制約が一部ある
比較的、形状やサイズの自由度が高い成形方法ですが、金型を使用している限り、成形後に型から上手く抜ける形状(「抜き勾配」という)にしなければならないという制約があります。また、極端な偏肉(厚肉や薄肉)の成形は、高精度な品質を保つことが難しく不向きです。
③金型製作に時間とコストがかかる
金型は製品ごとに必要となるため、数ヶ月かかることが通例であり、また、その製作費用もサイズ・形状の多様さから高額となることが多いです。ただし、一度製作した金型は数年間は使用できるため、ランニングコストは抑えることが可能です。
射出成形特有の不良とその解決策
偏肉
樹脂をキャビティ(金型内部の凹部空洞)内に射出充填する際、「偏肉」という製品の肉厚違いとなる形状欠陥を招くことがあります。なお、偏肉は、金型の精度や構造、強度(コアの倒れ、キャビティ(金型内部の凸部空洞)とのズレなど)が主な原因となり、肉厚が薄い成形品や深さが深い成形品によく見られる不良現象です。この偏肉を防止するためには、成形条件変更による肉厚調整や金型の追加工・改造などが必要となります。
そり変形
金型内で不均一な収縮差が発生すると、「そり変形」という不良を招き、部品の寸法精度低下による組み付け時のはめ合い不良や外観不良の原因になります。なお、そり変形とは、金型から製品を取り出した後、変形する現象のことで、その発生要因として次の2つの要因が考えられます。
1つ目は、成形品の冷却時において、成形品の形状や金型内温度分布によって成形品各部の冷却速度差が生じ、これによって材料の収縮に差が生じてそり変形が生じる熱要因です。
2つ目は、金型内を流れる樹脂の流速差によってせん断応力が生じ、分子鎖や強化繊維などのフィラーが配向し、物性値の異方性や分布が生じて冷却時に収縮差が発生し、そり変形が生じる流動要因である。このそり変形を抑制するためには、金型の設計変更や成形条件の最適化が挙げられますが、効率的に対策をするためには,射出成形品のそり変形を事前に予測することが重要となります。
ウェルドライン
射出された樹脂が金型内で一旦分岐し、再度合流する際、「ウェルドライン」という不良を招き、成形品の強度低下や外観不良の原因になります。なお、ウェルドラインは金型内で各方向に分岐した樹脂流動が、合流する際にうまく混ざらずにラインを生じてしまう現象で、開口部を有する成形品や肉厚の変化が大きい成形品や複雑な形状の成形品で多く見られます。
このウェルドラインを防止するためには、合流する際の金型温度を調整することが必要となります。